活性炭を自由自在に成形する ~真空ポンプの排気性能を向上~
研究キーワード
活性炭 , 多孔質材料 , 自由成形 , SPS , Spark Plasma Sintering , 吸着
研究概要
核融合発電は、1億度を超える高温プラズマに水素燃料を注入し、注入された水素が高温のイオンとなって核融合反応を起こすことで成立します。イオン化した水素(燃料粒子)は時間の経過とともにプラズマの外に排出され、一部はプラズマを閉じ込める容器の壁で跳ね返って再びプラズマに戻ったり、また一部は真空ポンプによって容器の外に排出されたりします。その真空ポンプの一つとして、核融合実験装置では、極低温真空ポンプ(クライオポンプと言います)が使われています(図1)。クライオポンプを、ダイバータと呼ばれる燃料排出システム内で用いることで、プラズマに戻る水素を減らすことができます。クライオポンプには、無数の細かい孔を持つ活性炭が張り付いた吸着パネルが内蔵されています。活性炭をマイナス250℃以下に冷やすと、水素燃料を排出する機能を発揮するようになります。
これまで、クライオポンプの吸着パネルに用いられている活性炭には、以下の問題点や改善要望がありました。
① 形状的な制約がある(ペレット型、粉体、シート等に限られる)
② 熱伝導性が悪い(ペレットでは有機物等のバインダーを含むため)
③ 強度が低い(吸着パネルからの脱落・剥離等)
そこで、私たちは SPS (Spark Plasma Sintering)法を用いることで以下のような開発材の作製に成功しました。
① 板状やブロック状の固形体(多孔質体)が作製可能(図2)
② 固形化しても、原料粉体が元来有する細孔特性を損ねない
③ バインダレスでの焼結が可能(活性炭100%)
④ 高い熱伝導性(バインダレスのため)
⑤ 高い強度(吸着パネルとしての要求強度を満たす)
⑥ 気孔率の調整が可能(焼結条件や使用粉体の最適化)
このような新しい製造手法を用いることで、様々な特性の改善を見出すことができました。なお、本技術シーズは東邦金属株式会社と共同で特許を取得しています(特許情報参照)。現在、クライオポンプとしての特性を把握するため定量評価を実施しているほか、更なる付加価値を見出すべく、第二成分の添加等によるハイブリッド化も視野に入れ、研究・開発を進める予定です。さらに本件開発技術を活用し、クライオポンプに限定せず、様々な用途の活性炭製品群に挑戦して参ります。
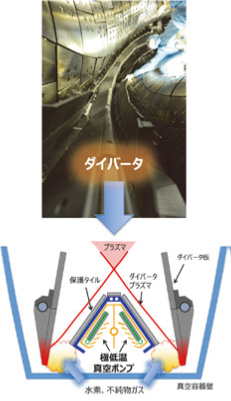
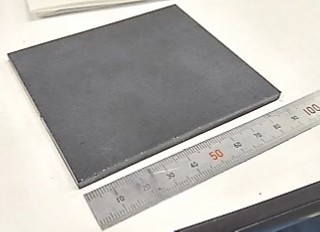
想定される応用先・連携先
高性能な真空ポンプは、半導体製造過程において革新的な役割を担うことと考えられます。半導体の製造過程では真空状態での製造が必要となっており、クライオポンプが使用されています。本技術によりクライオポンプに適した活性炭を成形することができれば、市販品の活性炭よりも排気性能を大幅に改善できます。その結果、クライオポンプの連続稼働時間を増やすことができ、半導体製造の長時間の連続運転が可能となり、メンテナンス時間を削減することでランニングコストを抑えることができます。
アピールポイント
• 最大のアピールポイントは、自由自在に活性炭を成形できる点です。
• 活性炭は真空ポンプだけではなく、吸着性能を利用して様々な用途で使用されています。これまで固形化できずにいた活性炭材料でも本技術によって成形することができます。
関連する特許出願番号・特許番号
特許番号:特許第7016080号
発明の名称:活性炭を含有する焼結体及びその製造方法